Essential Machines for High-Efficiency Fertilizer Manufacturing
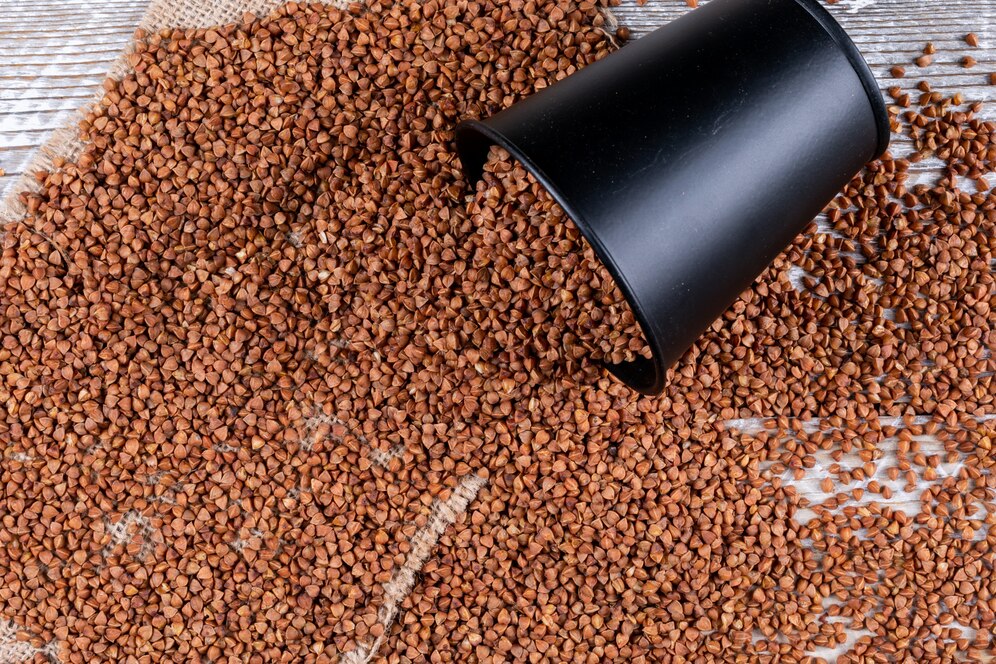
The foundation of any fertilizer production line lies in its NPK making equipments, which transforms raw materials into nutrient-rich granules. These systems typically include heavy-duty crushers for size reduction, precision mixers for homogeneous blending, and advanced granulators that form uniform pellets. Modern designs incorporate wear-resistant materials and automated controls to ensure consistent output.
Granulation Technologies in NPK Production
Central to NPK compound fertilizer equipment are the granulation methods that determine product quality. Rotary drum granulators dominate the industry, achieving 90-95% efficiency in converting powder mixtures into 2-4mm granules. Alternative systems like disc pelletizers offer better size control for specialty formulations, while extrusion granulators handle moisture-sensitive materials without drying requirements.
Material Preparation Systems
Before granulation, raw materials undergo rigorous preparation. Primary crushers reduce ammonium nitrate, phosphate rock, and potash to 20-80 mesh particles. Vibrating screens then remove oversized materials, while computerized batching scales measure ingredients with ±0.5% accuracy. This precision ensures the exact N-P-K ratios required for different crop nutrition formulas.
Drying and Cooling Processes
Post-granulation treatment is critical in NPK making equipments. Rotary dryers with indirect heating systems reduce moisture to <1.5% without nutrient degradation. Counter-flow coolers then stabilize granule temperature before coating. Modern designs incorporate heat recovery systems that capture 20-30% of thermal energy, significantly reducing fuel costs.
Automation in Modern Fertilizer Plants
Today's NPK compound fertilizer equipment features sophisticated control systems. PLCs monitor and adjust parameters like steam pressure, drum speed, and drying temperature in real-time. IoT sensors track equipment health, while automated sampling stations conduct quality checks without operator intervention. These technologies reduce human error while increasing production consistency.
Environmental Protection Features
Manufacturers now prioritize eco-friendly designs in NPK making equipments. Enclosed systems with pulse-jet dust collectors maintain workplace air quality below 5mg/m³. NPK drying equipment Ammonia scrubbers neutralize gaseous emissions, and noise enclosures keep sound levels under 85dB. Water recycling systems in granulation areas further minimize environmental impact.
Energy Efficiency Solutions
Modern NPK compound fertilizer equipment incorporates multiple energy-saving features. Variable frequency drives optimize motor speeds based on load requirements, reducing power consumption by 15-20%. Insulated dryer shells minimize heat loss, while heat exchangers recover thermal energy from exhaust gases. These innovations help plants meet stringent carbon emission standards.
Quality Control Mechanisms
Advanced monitoring systems ensure product consistency in NPK making equipments. Online moisture analyzers provide real-time data, while X-ray fluorescence (XRF) units verify nutrient content. Automated screening machines separate undersized or oversized granules, maintaining strict size specifications between 2-4mm.
Maintenance Requirements
Proper upkeep extends the lifespan of NPK compound fertilizer equipment. Daily tasks include bearing lubrication and inspection of granulator liners. Weekly maintenance involves cleaning heat exchanger surfaces, while monthly schedules cover gearbox oil changes and electrical system checks. Predictive maintenance software helps plan component replacements before failures occur.
Capacity Selection Guidelines
Choosing appropriate NPK making equipments requires evaluating production needs. Small-scale operations (1-5 t/h) benefit from modular designs, while large plants (15-30+ t/h) require heavy-duty, continuous systems. Key considerations include available space, utility infrastructure, and future expansion plans to avoid premature equipment obsolescence.
Safety Features for Operators
Modern NPK compound fertilizer equipment incorporates multiple protective measures. Emergency stop buttons are positioned every 5 meters, while gas detectors monitor for ammonia leaks. Anti-slip walkways, guarded moving parts, and automated lockout systems create safer working environments in potentially hazardous production areas.
Cost Considerations
Investing in quality NPK making equipments involves balancing capital and operating expenses. While premium systems command higher initial costs, their energy efficiency and durability typically deliver ROI within 2-3 years. Operational savings come from reduced downtime, lower maintenance requirements, and improved product quality that commands better market prices.
Emerging Technological Trends
The fertilizer equipment industry continues evolving with several innovations. AI-powered process optimization adjusts parameters in real-time for maximum efficiency. Robotic packaging systems increase bagging speeds while reducing labor costs. New coating technologies enhance nutrient release patterns, creating value-added products for precision agriculture.
Conclusion
Selecting the right NPK compound fertilizer equipment requires thorough evaluation of production requirements, raw material characteristics, and quality expectations. Partnering with experienced manufacturers ensures proper system design and integration. For optimal results, prioritize energy-efficient, automated systems with comprehensive after-sales support to maximize long-term productivity and profitability.
- Music
- Political
- Religion
- Ver Página
- News
- Sports
- Interior Design
- Personal Finance
- Book and Writing
- Art and Design
- Business
- Parenting
- DIY Craft
- Personal
- Photography
- Fashion and Beauty
- Lifestyle
- Health and Fitness
- Travel
- Food
- Outro